Heaptalk, Jakarta — Industry 4.0 has brought numerous technological innovations to maximize productivity and efficiency. However, the public, particularly in Indonesia, still holds misconceptions about Industry 4.0, believing it will replace human roles and harm the workforce. The workforce plays a crucial role in this revolution, and its value cannot be overstated.
According to Saiful Bahri, Head of Digital Industry Center (PIDI) 4.0, the industry 4.0 revolution does not substitute human roles with tools or autonomous systems. The digital transformation in the manufacturing sector aims to collaborate humans and machines/tools, with the Internet of Things as the core value of Industry 4.0.
“The role of humans in Industry 4.0 is still essential. The challenge we face today is building the competencies of the industrial workforce to adapt to the era of Industry 4.0, one of which is by developing 4.0-based competencies for existing and future industrial human resources,” Saiful emphasized.
Technology transfer and industrial competencies
The Ministry of Industry has mandated PIDI 4.0, under the Agency for Industrial Human Resource Development (BPSDMI), to continuously build public awareness of Industry 4.0, particularly by educating them through diverse training sessions, workshops, and seminars.
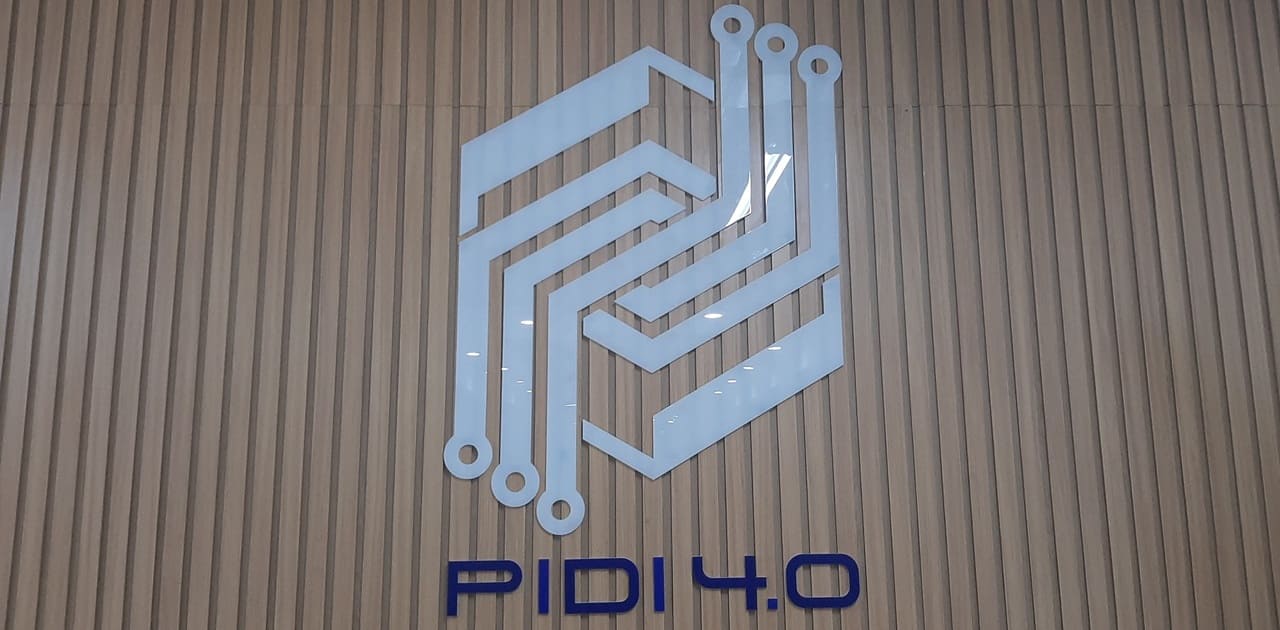
Moreover, the government is highly aware of the critical factors in digitalizing manufacturing, including technology transfer and industrial human resource competencies. Saiful stated that PIDI 4.0, with the government’s full support, aims to prepare a competent industrial workforce for Industry 4.0. This way, technology adoption can be accelerated to embody Making Indonesia 4.0.
According to Saiful, the manufacturing sector currently needs a highly motivated workforce that is constantly learning and adapting to Industry 4.0. He added, “Strong critical thinking, communication, innovation, solution-oriented, and continuous striving to develop 4.0 competencies are essential to meet the challenges of the Industry 4.0 era.”
To develop these abilities, PIDI 4.0 facilitates multiple training programs for the existing industrial workforce, including data analysis, lean manufacturing 4.0, Industry 4.0 transformation manager, Internet of Things (IoT) application engineering, IoT network engineering, Industrial Internet of Things (IIoT), PLC-based electronics equipment operation, and maintenance 4.0. There are also training programs for cloud computing engineers, data scientists, data analytics, mechatronics, pneumatics & hydraulics, and basic industrial robotics.